Calculation of Blow Room:
The section where the supplied compressed bale is turned into a uniform lap of a particular length by opening, cleaning, blending, or mixing is called blow room. It is the starting of the spinning operation where the fiber is opened, cleaned, mixed, micro dust removed, and evened thus passed to carding machine without increasing fiber rupture, fiber neps, broken seed particles, and without removing more good fibers. In this article, I have given the example with the calculation of Blow Room.
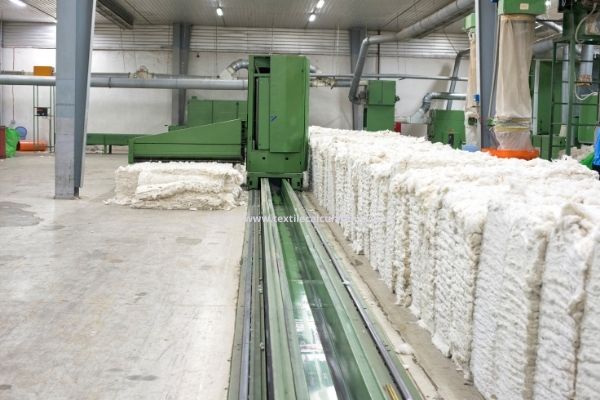
Production Calculation of Blow Room
* 1 lb = 16 ounce = 7000 grain = 453.6 gm.
* 1 Metric ton = 2204 lb.
* 1 kg = 2.2046 lb.
Problem-1:
A lap contains 2% trash after processed in B/R having a cleaning efficiency of 80%. Find the trash % in raw cotton.
Solution:
We know,
………………………………Trash remains after processing
Cleaning efficiency = …………………………………………….
…………………………………………….Total trash
…………………..2%
=> 80 = ………………….
…………….Total Trash
=> Total Trash = 2/100 x 80
=> Total Trash = 2.5%. (Ans.)
Problem-2:
Bottom calender roller dia = 7 inches, rpm = 10 & wt. of every yds lap is 12 oz and cleaning efficiency 75%. Find out the production of B/R per hour.
Solution:
…………………………………..3.14 x 7 x 10 x 60 x 75 x 12
Production/hr of B/R = ……………………………………….
……………………………………………….36 16 x 100
= 206.06 lb (Ans.)
Problem-3:
If lap length constant is 720, then set the change pinion for 40 yds lap.
Solution:
………………………….lap length constant
Change pinion = ………………………………..
………………………………….lap length
……720
= ………..
…….40
= 18 T (Ans)
Problem-4:
If lap wt. is 15 oz per yds, find the hank.
Solution:
………………1 yds x16 ounce
Hank = ……………………..………..
…………….840 yds x15 ounce
= 0.0012 hank. (ANS)
Problem-5:
If lap wt. – (a) 15 lb/yds, (b) 15 lb/m, (c) 15 grain/ yds, (d) 15gt/m, (e) 15gm/yd, (f) 15gm/m. Find the hank.
Solution:
…………………1 yds x16 lb
a. Hank = …………………….. = 0.0000793 hank. (Ans)
……………….840 yds x15 lb
………………….1 m x1 lb
b. Hank = ……………..……….
……………….840 yds x15 lb
……..1.1 yds x1 lb
= ………………………
…..840 yds x15 lb
= 0.0000873 (Ans)
……………….1 yds x 7000 grain
c. Hank = ……………………………… = 0.55 (Ans)
………………..840 yds x15 grain
………………..1 m x 7000 gr
d. Hank = …………………………
………………..840 yds x15 gr
….1.1 x 7000
= ……………….
……840 x15
= 0.611 (Ans).
………………1 yds x 453.6 gm
e. Hank = ……………..………… = 0.036. (Ans)
……………….840 yds x15 gm
……………..1 m x 453.6 gm
f. Hank = ………………………
……………..840 yds x15 gm
…..1.1 x 453.6
= …………………
…….840 x 15
= 0.0396. (Ans)
Problem-6:
Find the no. of lapper hour in scutcher m/c of Bottom calender roller dia = 7 inch, rpm = 12, efficiency 80%. Lap length 40 yds.
Solution:
………………………………π x 7 x12 x 80 x 60
Production of m/c = ………………………….. yds
…………………………………….36 x 100
= 351.85 yds.
……………………351.85
No. of lap = ………………
………………………40
= 8.79
= 9 (ANS)
Problem-7:
Find the no. of lap per hour in scutcher m/c of Bottom calender roller dia = 7 inch, rpm = 12, efficiency 80%, lap wt. 14 oz/yds.
Solution:
………………………3.14 x 7 x12 x 0.80 x 60 x 8 x 14
Production = ……………………………………..…………… lbs
…………………………………………36 x16
= 2461.76 lbs
…..2461.76
= ……………. metric ton
……..2204
= 1.117 metric ton. (Ans)
Problem-8:
If in a xsutcher m/c, rpm of B.C.R. is 10, dia 7 inches, lap wt. 12 oz/yd. Find the production/hr at 90% efficiency.
Solution:
……………………..3.14 x 7 x 10 x 12 x 60 x 90
Production = ………………………………………….. lbs
……………………………….36 x 16 x 100
= 247.275 lbs (ANS)
Problem-9:
Calculation of Blow Room line with 2 scutchers if B.C.R. dia = 7 inch, rpm = 10, Efficiency 90%, wastes 4%, lap wt. 14oz/yd.
Solution:
………………………3.14 x 7 x10 x1x 60 x 90 x (100 – 4) x 2 x14
Production = ……………………………………………..……………………. lbs
…………………………………….36 x 16 x 100 x 100
= 553.896 lbs. (Ans)
Problem-10:
Calculate production/he of a B/R line if, r.p.m. of B.C.R. = 14, Dis = 18 cm,, lap hank = 0.0012, efficiency 80%, no. of scutcher = 2.
Solution:
………………………3.14 x18 x14 x 60 x 0.80 x 2
Production = ………………………………….………….. lbs
………………………..36 x 2.546 x 840 x 0.0012
= 822.2 lbs. (Ans)
Problem-11:
Find the B/R cleaning efficiency, if the waste in Raw cotton = 6%, waste in sliver = 0.4%. Carding, cleaning efficiency 75%.
Solution:
…………………………………………..waste in lap – waste in sliver
Carding cleaning efficiency = ………………………..………………… X 100
………………………………………………………..waste in lap
……………x – 0.4
=> 75 = …………. x 100
………………..x
=> x = 1.6%.
………………………………………6 – 1.6
B/R cleaning efficiency = …………….. x 100
……………………………………………6
= 73% (Ans.)
Problem-12:
The trash control of feed cotton is 3%. After passing the beater 2% waste is extracted, of which 15% is good fibre, what is the cleaning efficiency of the beater?
Solution:
……………………………..100-15
2% waste extraction, ……..…… x 2 = 1.7% of the original trash has been taken out by beater.
………………………………..100
(3-1.7) = 1.3% trash remains in the mtls, which are delivered from the beater.
…………………………………Original T.C – T.C. in delivered cotton
Cleaning Efficiency = ……………………………………………………………. x 100
………………………………………………………Original T.C
…..3-1.3
= ……….. x 100
………3
= 56.66% (Ans.)
Problem-13:
Find out beats/inch from the following data- Beater r.p.m. = 720, no. of striker = 16, Feed roller r.p.m. = 24, Dia of feed roller = 3 inch.
Solution:
Beats / min = Beater r.p.m. x no. of striker
= 720 x 16 no.s
= 11520 no.s
Surface speed of feed roller = π DN
= 3.14 x 3 x 24
= 226.08
……………………….11520
Beats / inch = ……………….
………………………226.80
= 50.96 (Ans.)
Problem-14:
The trash content of cotton as fed to Beater 3.6%. The waste extraction is 1.5% of which 80% is trash. What is the cleaning efficiency of the beater?
Solution:
…………………………………80
1.5% waste extraction, ……… x 2 = 1.2% of the original trash has been taken out by beater.
………………………………..100
(3.6-1.2) = 2.4% trash remains in the mtls, which is delivered from the beater.
…………………………………Original T.C – T.C. in delivered cotton
Cleaning Efficiency = …………………………………………..………………… x 100
……………………………………………………….Original T.C
…..3.6-2.4
= …………… x 100
……..3.6
= 33.3% (Ans.)
You may like also: How to Find Out the Production of the Blow Room Line